The purpose and precautions of electro-hydraulic servo testing machine.
The electro-hydraulic servo testing machine is a high-precision, high-reliability material mechanical testing equipment, which is widely used in industry, construction, aviation and other fields.
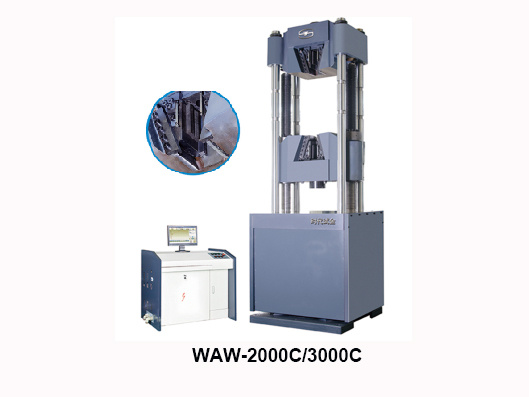
Its core function is to accurately control the load and deformation through the electro-hydraulic servo system to achieve a comprehensive evaluation of the mechanical properties of the material. The following is a comprehensive analysis of its specific uses and precautions for use:
1. Main uses
Material mechanical properties testing
Tensile and compression tests: used to determine the tensile strength, yield strength, elastic modulus and other parameters of metals and non-metallic materials, such as steel, concrete, plastics, etc.
Fatigue performance research: simulate the actual working conditions through cyclic loading, evaluate the fatigue life and fracture behavior of the material, and is suitable for aviation components, bridge structures and other fields that are subjected to long-term dynamic loads.
High load testing: can meet the strength verification needs of large steel components and heavy machinery parts, such as steel bars and steel strands for construction.
Quality control and process optimization
In the steel, automobile manufacturing and other industries, it is used to verify the effects of heat treatment and rolling processes to ensure that the hardness and strength of the material meet the standards (such as GB/T 700, ISO 6892).
Mechanical property testing of welded joints and special alloys (such as high chromium steel and titanium alloy) to avoid structural failure caused by material defects.
Scientific research and standard verification
Supports a variety of international standards (such as ISO 7500, ASTM E8) for performance comparison and standard compliance testing in the material research and development stage.
2. Precautions for use
(I) Operation specification
Jig selection and installation
The adapter jig must be selected according to the sample type (such as standard sample, steel strand) to avoid sample slippage or jig damage due to mismatch of the jig.
For superhard materials (such as spring steel), special material clips are required to prevent surface scratches.
Test parameter setting
Reasonably set the load, deformation rate and number of cycles to avoid data deviation or equipment damage caused by overload or parameter errors.
Loading/unloading must be slow and uniform. It is strictly forbidden to move the crossbeam when applying force to prevent the drive mechanism from failing.
Safe operation
During the test, it is forbidden to place your hands in the test area. In case of emergency, the emergency stop button should be pressed immediately.
After the sample breaks, the fragments must be cleaned up in time to prevent the residue from interfering with subsequent tests or damaging the equipment.
(II) Maintenance
Cleaning and lubrication
After each test, dust and metal debris must be thoroughly removed to prevent them from entering the hydraulic system and causing valve hole blockage or piston scratches.
Regularly apply lubricating oil to the screw and transmission parts to reduce dry friction loss.
Hydraulic system management
The hydraulic oil level needs to be checked regularly and replaced every 2000-4000 hours. The oil temperature must not exceed 70°C (the cooling system needs to be started if it exceeds 60°C).
The filter should be replaced every 6 months (without blockage indicator) or replaced according to the alarm prompt (with indicator).
The accumulator pressure must be kept normal and only nitrogen is allowed to be filled.
Component inspection
Regularly inspect key components such as pressure valves, flow valves, and travel switches to ensure that the signal device is sensitive and reliable.
The cooler needs to be cleaned of scale regularly (air cooling) or copper pipe leakage (water cooling).
(III) Equipment stability guarantee
Fastener inspection: The vibration caused by the fracture of the specimen can easily cause the bolts to loosen. It is recommended to check the fasteners every 30 working days to prevent structural damage.
Abnormal monitoring: pay attention to external leakage, abnormal noise (such as pumps, couplings) and pollutants, and promptly check for hidden dangers.
3. Typical application scenarios
Steel industry: detect the uniformity of hot-rolled steel plates and verify the strength of high-alloy steel welds.
Construction engineering: evaluate the compressive strength of concrete and the tensile properties of steel bars.
Aerospace: analyze the fatigue life of composite materials and the tensile properties of titanium alloy parts.
The electro-hydraulic servo testing machine has become a core tool for material mechanics analysis through precise load control and multi-functional testing modules. Its efficiency depends on standardized operation and system maintenance, such as reasonable selection of fixtures, regular replacement of hydraulic oil, and strict cleaning procedures. Users need to develop an operation plan based on specific test requirements (such as standard compliance, high-load testing), and follow the maintenance guidelines provided by the manufacturer to extend the life of the equipment and ensure data reliability.